
For a stable operation, these disturbances must be compensated accurately.
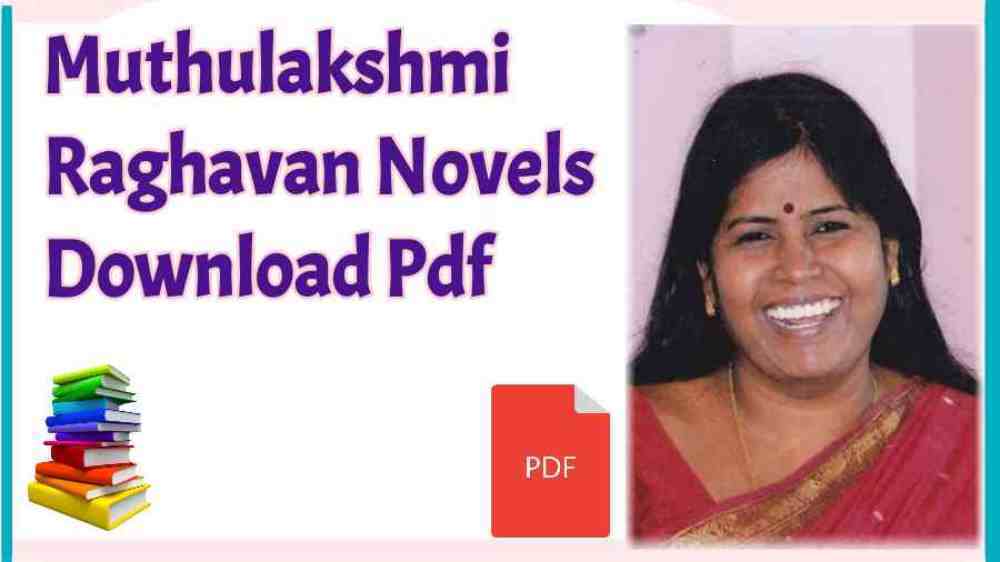
During the hover operation helicopters suffer from unknown external disturbances such as wind and ground effect. Numerous control techniques are developed for miniature unmanned helicopters to do hover operation with each method having its own advantages and limitations. Future improvement directions are also pointed out. The mathematical models of the system components (tank, pump, valve, to name a few) are experimentally determined (that is, identified) in order to help the controller design.Those controllers are used in the real plant, and the results are evaluated. Industrial control techniques are tested in the system, and the dynamics can be varied by opening and closing the manual valves in the piping network. The controllers are implemented in a computer, by the software MATLAB/Simulink.
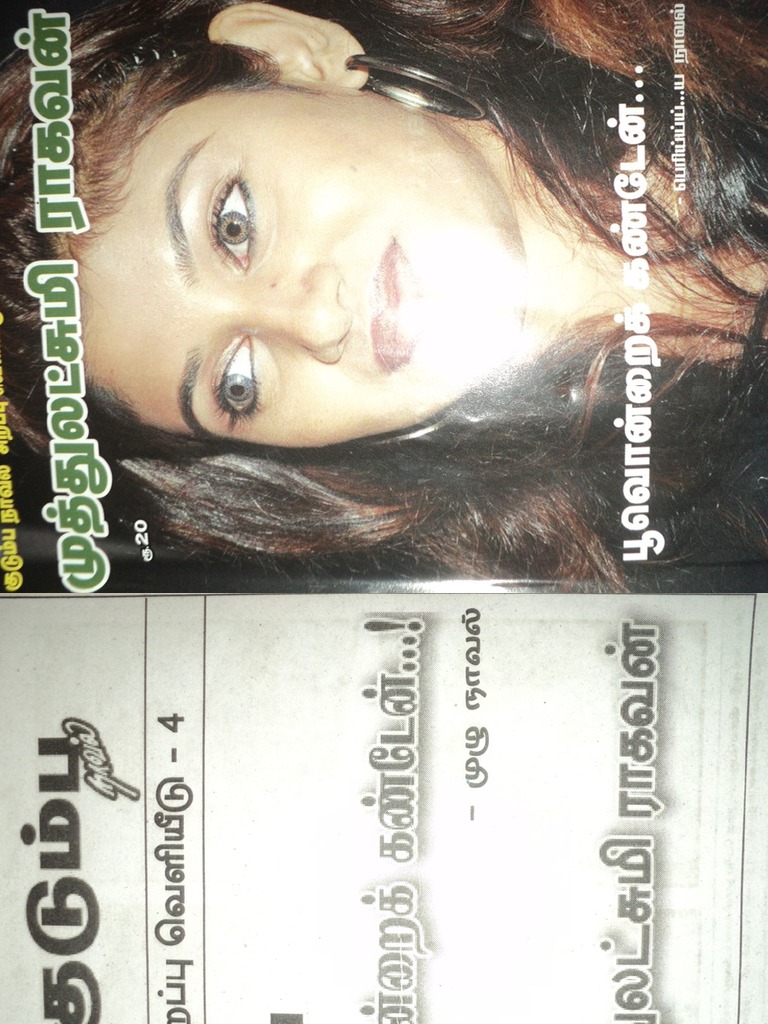
This board is also used to deliver control signals to the actuator (as an digital to analog converter). Those sensors deliver voltage signal that are proportional to the measured variable, and an analog to digital converter (acquisition board) is used in order to be used by control algorithms. There are four different (industrial standard) sensors for the variables above mentioned, that are: turbine sensor (water flow), pressure sensor, PT100 (temperature) and ultrasound (liquid level).
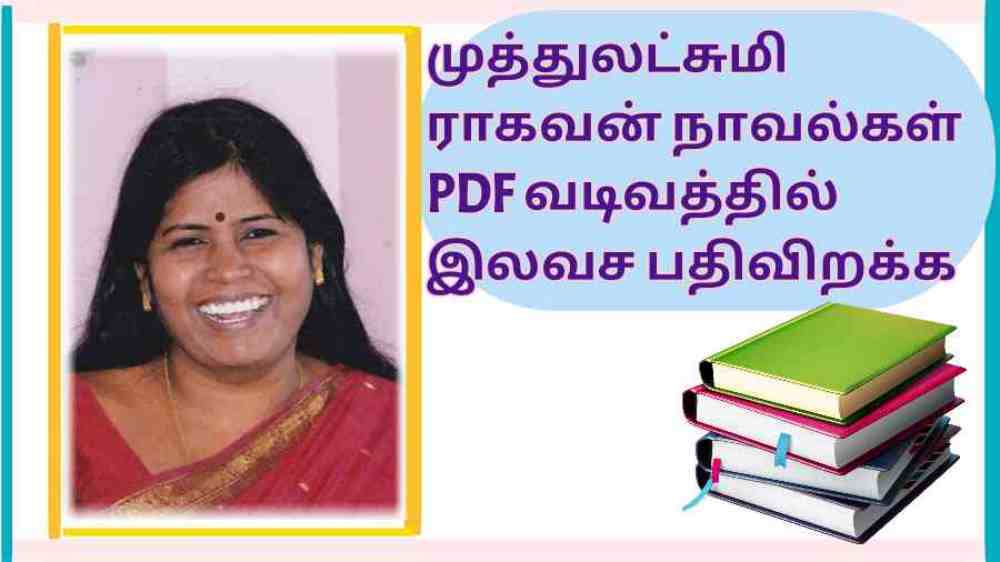
A proportional pump, which is the main actuator, forces (distilled) water through the piping system, which allows closed loop control of several physical variables, like water flow, temperature, water pressure and liquid level in one tank. This plant consisting of a pvc piping network connecting two reservoir tanks.
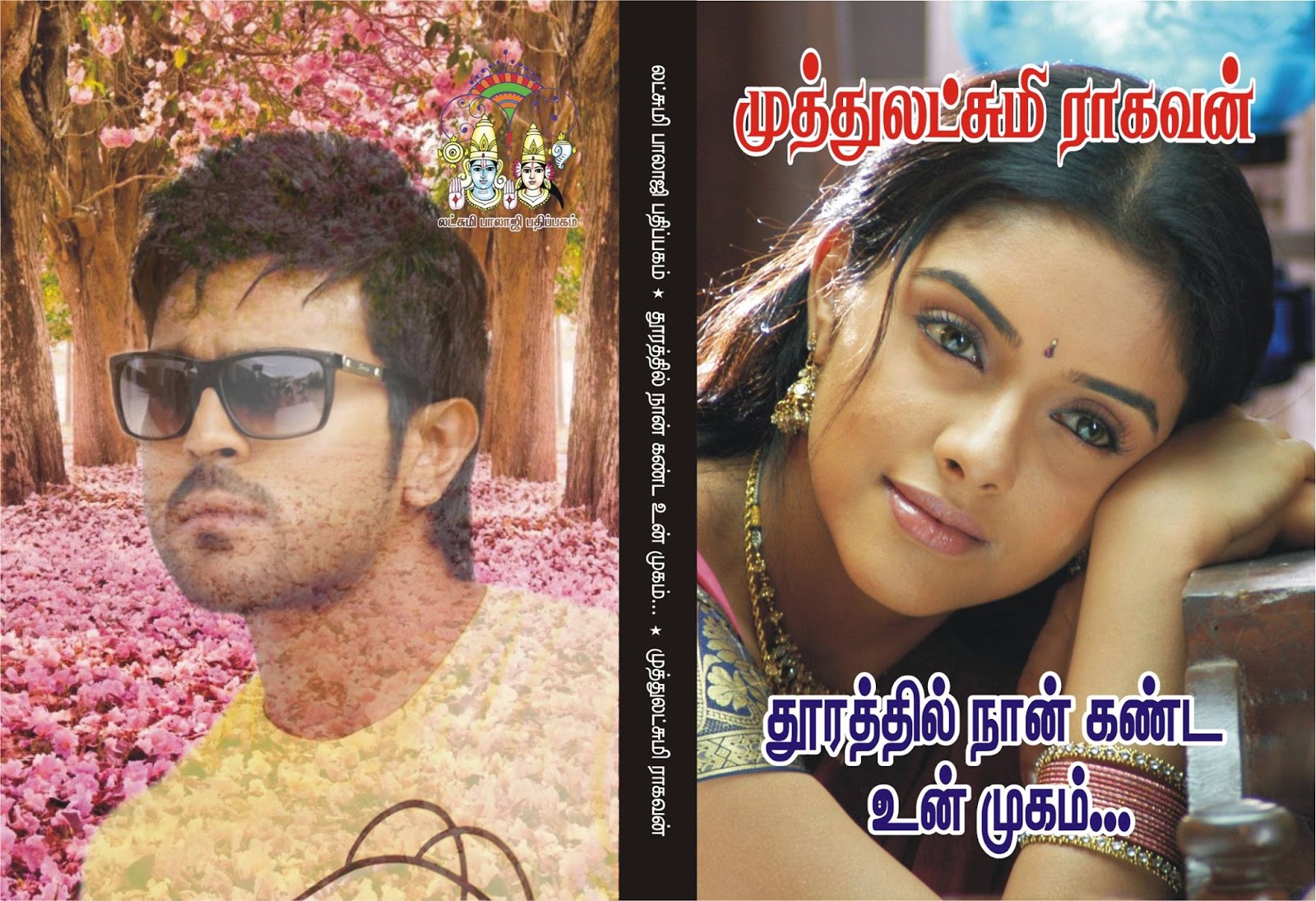
In this paper, nonlinear models are obtained and closed loop controllers are designed for a didactical fluid plant in order to be used in process control undergraduate courses.
